Automation Solution for Steel Plant
1. Project Details:
Industry: Metals
Location: Joda, Odisha
Project Duration: 3 months
Team: Client – 1 engineers; MWA: 2 engineers
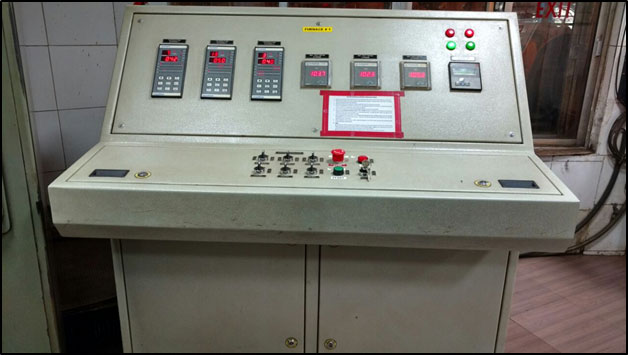
Need of the project:
- The entire plant was completely operated manually. Due to increase production demands in the market there was a huge dependency on man power leading enormous delays, rejection and production loss.
- Optimizing of energy consumption to save cost of power
2. The Problem:
- Due to manual operation system accuracy was dependent on manpower leading to product rejection, loss in production
- Reduction in cost of power
- Collecting data at high speed and high volume for analysis of process variables & trends
- Reduce downtime, quality issues and inefficiencies affecting the bottom line.
3. The Solution:
- Compact Logix Redundant PLC system to avoid system failure, data loss, improved system accuracy and increased production
- FactoryTalk SCADA based system for plant Visualization & monitoring of key power parameters
- FactoryTalk Historian to handle high-speed time-series data. Improve decision making related to process, time, and material management by comparing variances to targeted parameters.
- FactoryTalk VantagePoint to provide information in a context that enables analysis at-a glance. Operators as well as executives can share this data and make real time or predictive decisions based on correlations and trends revealed by the VantagePoint to reduce power & down time.
Features Offered:
- SMS alerts for critical data
- Customized Batch Reports
- Database connectivity & data exchange between plant and head office
- Easy analysis of high speed and volume data
- Real-time KPI data for all stakeholders
- Pre-configured reports and dashboards
- Web-based access to all critical data
- Monitoring of all essential plant KPI’s
- Monitoring motor current from 150 devices
- Monitoring power parameters from 120 devices
Scope of Work:
- Designing, erection & commissioning of Automation system
- Dismantling all the existing manual control panels & replacing it with new control panels
- Installation of Server Computer
- MIS integration (Historian and Vantage point). Designing of dashboards, trends & reports
- Data connectivity and data exchange between plant & head office
BOM:
- PLC Control Panel – 1 Set
- RIO Control Panel – 2 Sets
- Weight Indicator – 4 Nos
- Load Cells – 6 Nos
- Current Meters – 40 Nos
- Temp. Scanner 16 Inputs – 3 Nos.
- Commercial grade Computer – 2 Nos
- Industrial grade Computer – 1 No
4. The Results:
- Due to Automation, system accuracy has improved with no dependency on man power leading to increased production, reduction in downtime and better product acceptance in the market.
- 10-12% power saving resulting in around a profit of Rs. 8-10 Lakhs
- Better decision making due to availability of necessary KPI’s 24×7
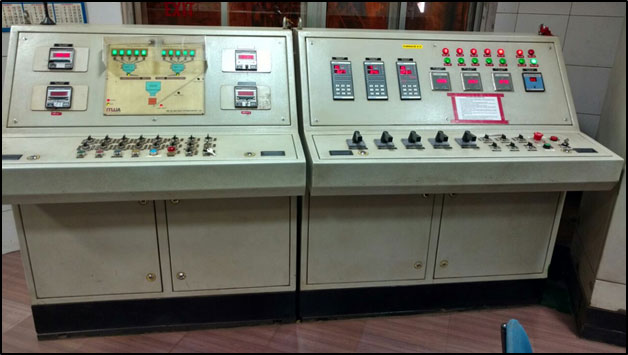
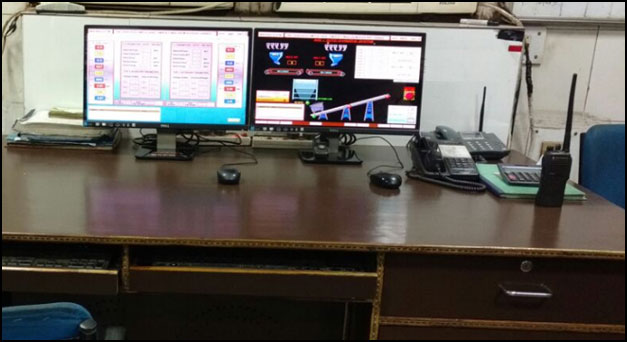
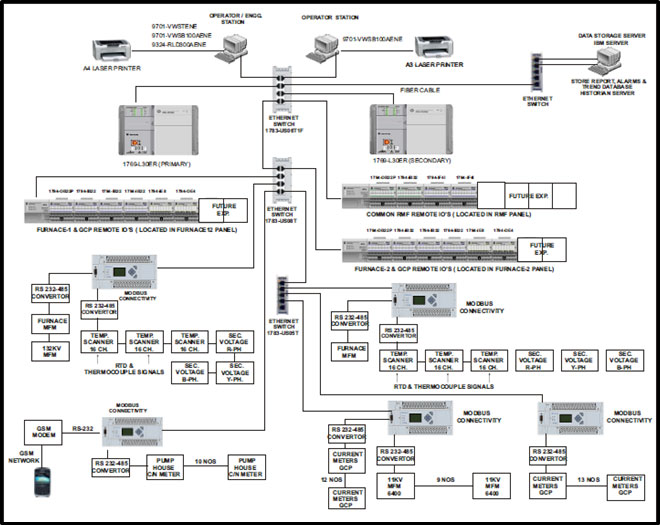